A Comprehensive Guide to the Sorts Of Ceramic Coating on the Market
Ceramic coverings have emerged as a critical remedy across numerous industries due to their one-of-a-kind buildings and applications. As we discover the distinct features and applications of these finishings, the implications for efficiency and long life become progressively noticeable, elevating inquiries about which type could best fit your demands.
Understanding Ceramic Coatings
Ceramic coatings are advanced safety options that have gained popularity in numerous sectors, especially in automotive and aerospace applications. These finishings are composed of a fluid polymer that, when healed, forms a resilient, hydrophobic layer externally of the substratum. This layer offers enhanced resistance to environmental contaminants, UV radiation, and chemical direct exposure, consequently expanding the life and visual allure of the underlying material.
The basic component of ceramic finishings is silica, which adds to their firmness and toughness. The application procedure usually includes surface prep work, application of the finishing, and treating, which can be attained with warm or UV light. When treated, ceramic finishes display outstanding bonding properties, allowing them to adhere highly to a variety of surface areas, including steels, plastics, and glass.
Along with their protective attributes, ceramic finishings likewise use convenience of upkeep. Their hydrophobic nature decreases the adherence of dirt and crud, making cleaning easier and much less frequent. Overall, the adoption of ceramic layers stands for a considerable advancement in surface area protection technology, offering both useful and visual advantages throughout numerous industries.
Kinds of Ceramic Coatings
Numerous kinds of ceramic coatings are readily available, each developed to satisfy details performance requirements and applications - Paint Protection Film. One of the most usual types consist of:
Silica-based Coatings: These finishings primarily contain silicon dioxide and are known for their toughness and chemical resistance. They are extensively utilized in automobile and industrial applications.
Titanium Dioxide Coatings: Prominent for their photocatalytic buildings, titanium dioxide finishings are frequently used in environments where self-cleaning and antifungal buildings are desirable, such as in structure materials and auto surfaces.
Zirconia Coatings: Identified by their high-temperature security and thermal resistance, zirconia finishings are utilized in applications such as generator engines and high-performance automobile components.
Alumina Coatings: Displaying excellent hardness and thermal security, alumina finishes are frequently utilized in wear-resistant applications, including reducing tools and industrial equipment. - Paint Protection Film
Crossbreed Coatings: Incorporating the residential or commercial properties of different products, hybrid finishes supply boosted efficiency attributes, making them suitable for one-of-a-kind and requiring applications.
Each sort of ceramic finishing offers distinctive functions, allowing users to pick the most proper remedy based upon certain ecological problems and efficiency demands.
Advantages of Ceramic Coatings
Ceramic layers, in specific, deal numerous benefits that make them significantly popular amongst producers and consumers alike. These coatings are immune to scratches, chemicals, and UV pop over to this site rays, guaranteeing that the underlying surface remains safeguarded over time.
Along with toughness, ceramic coatings offer exceptional hydrophobic homes, permitting very easy cleaning and maintenance. This water-repellent nature decreases the adherence of dirt, crud, and various other contaminants, which can lengthen the visual appeal and functionality of the surface area. Moreover, ceramic finishes can significantly improve thermal resistance, making them excellent for applications that endure heats.
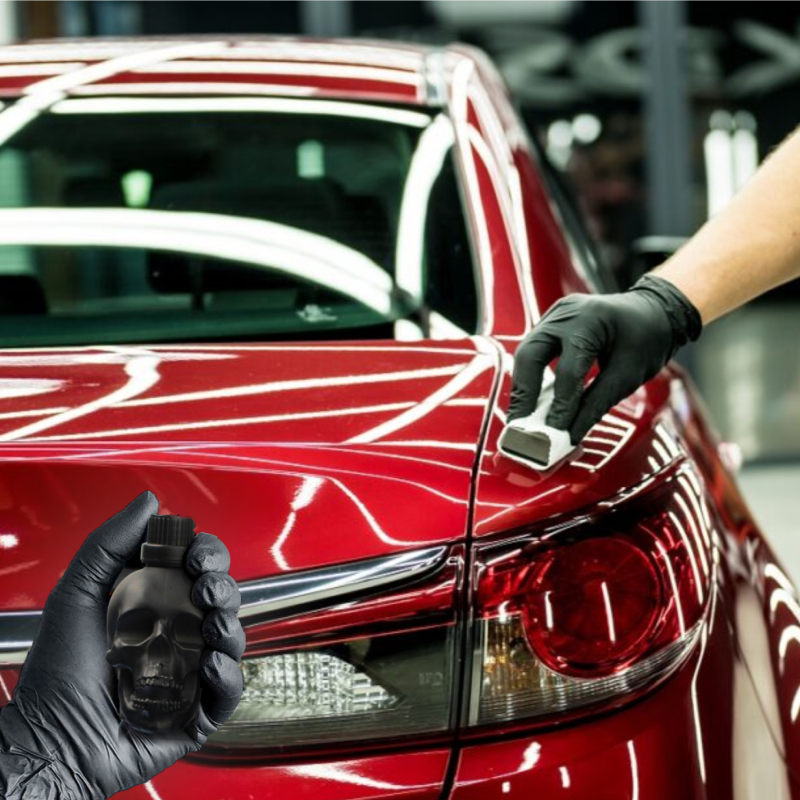
Application Process
When applying ceramic finishes, a meticulous strategy is vital to accomplish optimal outcomes. The application procedure normally starts with extensive surface area preparation. This includes washing, sanitizing, and polishing the surface to eliminate all impurities, including dirt, oil, and prior waxes or sealers. A tidy surface ensures proper attachment of the finishing.
As soon as the surface area is prepped, the next action is to use the ceramic finishing. The covering needs to be used in slim layers, as thicker applications can lead to unequal surfaces.
After application, the finish needs a specific treating time, commonly ranging from a couple of hours to a complete day, relying on the product. During this time, it is vital to prevent direct exposure to moisture or impurities. Lastly, a mild buffing may be necessary after treating to boost the gloss and get rid of any type of high spots. Following these steps carefully will maximize the performance and long life of the ceramic covering, supplying a resilient protective layer for the surface.
Maintenance and Longevity
To make sure the long life and efficiency of a ceramic finish, routine upkeep is vital. Ceramic finishings, understood for their durability and safety top qualities, need particular care routines to maximize their lifespan and performance. The initial action in upkeep entails regular washing with pH-neutral soap, staying clear of severe chemicals that can weaken the covering. It is advisable to clean the lorry on a regular basis, preferably every 2 weeks, to stop the build-up of contaminants that might jeopardize the layer's stability.
Along with routine washing, routine inspections are vital. Look for indicators of get more wear or damage, such as hydrophobic residential or commercial properties reducing or surface area flaws. If needed, a light polish may be related to invigorate the layer without stripping it away.
Furthermore, the application of a booster spray can boost the finishing's hydrophobic impacts and recover its gloss. This is particularly a knockout post beneficial for layers that have remained in usage for an extended period. Eventually, by adhering to these maintenance methods, one can substantially extend the life of a ceramic layer, making certain that it continues to provide optimum protection against environmental variables and maintain the visual appeal of the lorry.
Verdict
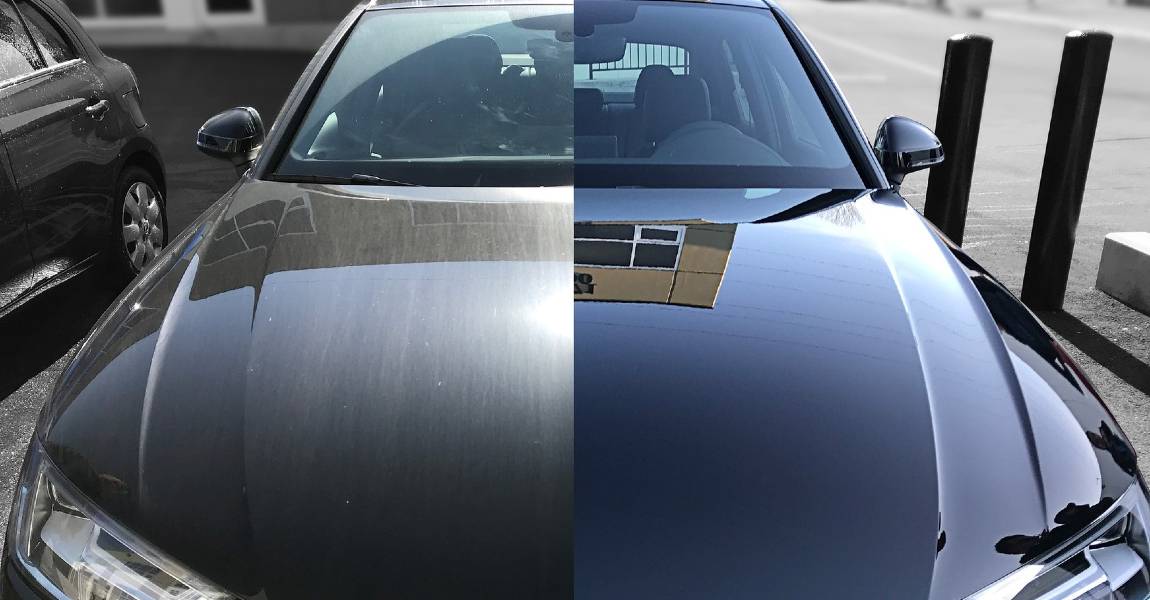